STRATIFICATION CONDITIONS
STRATIFICATION RESULTS
- Heating: 65°F during occupied hours; 55°F night/weekend/holiday temperature setback
- Ventilation: 0.06 cfm/ft2 during occupied hours (to meet ASHRAE Standard 62.1-2007)
- Stratification: 4˚F
- Air Conditioning: Not included in the analysis
HEATING OPERATING SCHEDULE
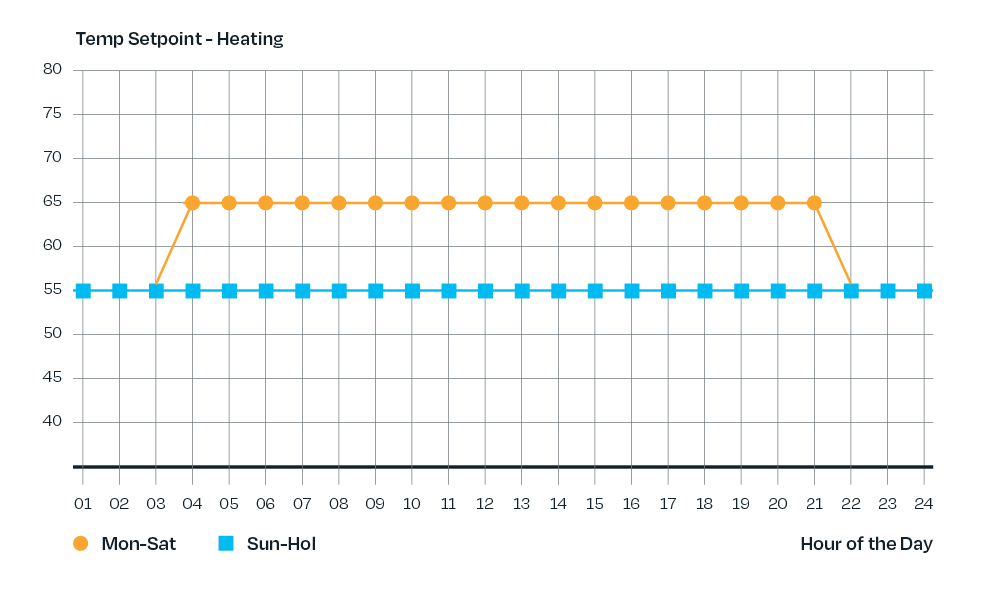
STANDARD CONDITIONS
COMPUTER MODELING RESULTS
Energy Comparison for Heating Systems Standard Conditions
Equal Stratification for All Systems (4°F), ASHRAE 62.1 Ventilation (0.06 cfm/ft2)
Energy Consumption |
Gas (Therms) |
Fan Electric (kWh) |
ASHRAE 90.1 Baseline |
30,907 |
76,733 |
Blow-Thru |
20,220 |
5,758 |
Draw-Thru |
25,052 |
7,317 |
Recirculation |
25,910 |
52,644 |
Unit Heater |
30,481 |
16,289 |
Air Turnover |
26,822 |
17,153 |
Infared |
32,156 |
11,164 |
Blow-Thru Space Heater
-
More energy efficient
-
Burner is downstream of blower
-
Components in the cold air stream
-
160oF max temp rise/discharge temp
-
Highest Btu/cfm ration
% Savings Vs. 90.1 Baseline
Blow-Thru |
34.6% |
92.5% |
Draw-Thru |
18.9% |
90.5% |
Recirculation |
16.2% |
21.4% |
Unit Heater |
1.4% |
78.8% |
Air Turnover |
13.2% |
77.6% |
Infared |
-4.0% |
85.5% |
Blow-thru heaters used 35% less natural gas and 93% less fan electricity than the ASHRAE 90.1 baseline heating system.
Blow-thru heaters used the least amount of total energy. Using any other heater type increased total therms required to heat the warehouse by 24% to 59%
% Increase Vs. Blow-Thru
Draw-Thru |
23.9% |
27.1% |
Recirculation |
28.1% |
814.2% |
Unit Heater |
50.7% |
182.9% |
Air Turnover |
32.6% |
197.9% |
Infrared |
59.0% |
93.9% |
Infrared heaters were auto-sized by EnergyPlus to handle the total heating load. Analysis and load did not incorporate the practice of keeping the space thermostat set 15-20% lower in order to save energy.
ELECTRIFICATION CONSIDERATIONS
EMISSION ANALYSIS OF ELECTRIC RESISTIVE HEAT FOR HIGH BAY SPACES
Electrification has been a growing trend as many stakeholders strive to reduce their carbon footprint. In addition, many localities are enacting legislation and corporations are setting policies that would prohibit natural gas heating. This results in many building owners providing electric resistive heat due to it being the lowest first cost option for heating high bay spaces using electricity. This typically results in a large increase in total carbon emissions as most electrical grids in the United States are still largely reliant on fossil fuels to generate electricity.
Cambridge Air Solutions has performed the following analysis in 2024 as an addendum to the study to compare the emissions that would be generated if some of the technologies in this study were revised from indirect fired gas heat to electric resistive heat.
- Compare direct gas fired, high temperature rise blow-thru heating system to commonly used electric resistive heating options
- Assume equal heating output for electric resistive option compared to the equivalent indirect fired system from GARD Analytics study.
- Corrected for efficiency difference between indirect gas fired technology and 100% efficient electric resistive heat
- Total MWh includes electricity usage from supply fan(s) and the electric heating element
- Assuming National Average Emission Rate of 852.3 lb CO2/MWh*
System |
Total Therms |
Total MWh |
Carbon Emissions (lbs.) |
Increased Carbon Emissions *Scaled to Direct Fired Blow-Thru |
Direct Fired Blow-Thru |
20220 |
6 |
241168 |
1x |
Electric Unit Heater |
0 |
731 |
622832 |
2.58x |
Air Turnover w/ Electric Heat |
0 |
646 |
550469 |
2.28x |
Electric Infrared Heater |
0 |
765 |
651927 |
2.70x |
Conclusion
Because electricity generation in the US relies heavily on fossil fuels, simply switching to an electric resistive heating system was shown to greatly increase the total amount of carbon emissions. Gas fired heating equipment is a historically reliable and effective means of decarbonization. It is important to understand the total effects of electrification when determining if it is the right fit for your building. For more information on this topic please reference Cambridge Air Solutions White Paper, Electric vs. Gas Heat, which dives deeper into this topic.
STRATIFICATION
ANALYZING ENERGY EFFICIENCY WITH DESTRATIFYING SYSTEMS AND FANS
A potentially important energy issue for warehouse heating is temperature stratification. Warehouses typically have high open ceilings where significant differences in air temperature can occur between floor level and the ceiling due to lack of adequate air movement. High levels of stratification will waste energy. Reduced stratification is a claimed benefit of destratifying ceiling fans and three of the heating systems modeled in this analysis (Blow-Thru, Air Turnover and Infrared). Energy modeling software, including EnergyPlus, cannot predict the amount of stratification created by each heating system but it can determine the additional energy used for specific levels of stratification. Therefore each heating system was first modeled using just 4°F stratification and then a second set of modeling results were obtained for 10°F stratification to determine the predicted amount of additional energy used for those buildings that do not use a destratifying heating system or fans.
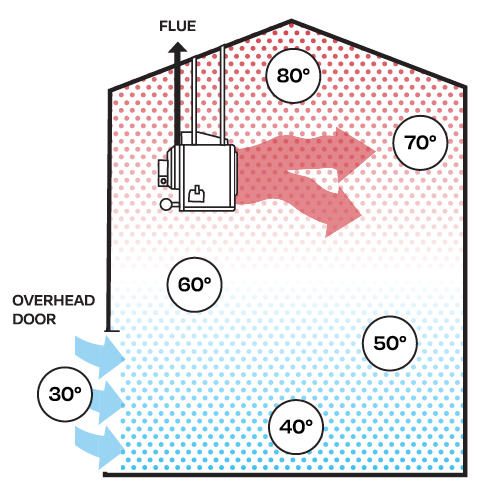
Blow-Thru Heaters Reduce Stratification
Building studies show small blow-thru type space heaters reduce stratification with their high velocity vertical throw diffusers. They achieve 3°F to 5°F temperature variation, which is the same of better than large air turnover systems while using much less energy.
COMPUTER MODELING RESULTS
Stratification Comparison
- 4°F Stratification for Blow-Thru, Air Turnover*, Infrared
- 10°F Stratification for all other systems
- ASHRAE 62.1 Ventilation (0.06 cfm/ft2)
Energy Consumption |
Gas (therms) |
Fan Electric (kWh) |
ASHRAE 90.1 Baseline |
30,907 |
76,733 |
Blow-Thru |
20,220 |
5,758 |
Draw-Thru |
25,052 |
7,317 |
Recirculation |
25,910 |
52,644 |
Unit Heater |
30,481 |
16,289 |
Air Turnover |
26,822 |
17,153 |
Infrared |
32,156 |
11,164 |
% Savings Vs. 90.1 Baseline
Blow-Thru |
34.6% |
92.5% |
Draw-Thru |
18.9% |
90.5% |
Recirculation |
16.2% |
21.4% |
Unit Heater |
1.4% |
78.8% |
Air Turnover |
13.2% |
77.6% |
Infrared |
-4.0% |
85.5% |
% Increase Vs. Blow-Thru
Draw-Thru |
23.9% |
27.1% |
Recirculation |
28.1% |
814.2% |
Unit Heater |
50.7% |
182.9% |
Air Turnover |
32.6% |
197.9% |
Infrared |
59.0% |
93.9% |
* Low velocity constant air turnover units require 2-3 building air turnovers per hour to minimize stratification.
VENTILATION RATE
MEETING ASHRAE 62.1 VENTILATION STANDARDS
ASHRAE Standard 62.1 requires a continuous supply of ventilation air at the minimum rate of 0.06 cfm/ft2 for warehouse applications during periods of occupancy. This is a prerequisite for all LEED projects and is also required by many local codes. All seven heating systems were modeled to meet this ventilation requirement. A 30% higher ventilation rate of 0.078 cfm/ft2 will earn an indoor environmental quality credit point for LEED projects. An additional set of modeling results was obtained for this condition to determine its impact on energy use.
INDOOR ENVIRONMENT QUALITY (INDOOR AIR QUALITY - IAQ)
Minimum IAQ Performance (Prerequisite)
Intent - LEED Certified buildings must meet the minimum requirements of Sections 4 through 7 of ASHRAE Standard 62.1 or applicable local code whichever is more stringent. ASHRAE 62.1 requires a continuous ventilation rate of 0.06 cfm/ft2 during occupied periods for most warehouse applications.
EQ Credit 2: Increase Ventilation (Potential Points: 1)
Intent - Provide more outdoor air ventilation than that required by ASHRAE 62.1 to improve indoor air quality. For mechanically ventilated spaces this means increasing the ventilation rate by at least 30%. For most warehouse applications this would require a continuous ventilation rate of 0.078 cfm/ft2 during occupied periods.
Warehouse Heater Contribution
Direct gas-fired heaters certified to ANSI Standard Z83.4 can help meet this requirement because they use only 100% non-recirculated outside air. Consult with the heater manufacturer to explore the best options for this credit. This may be a “free point” if the heating equipment already has the capability to provide 0.078 cfm/ft2. However, it may not make sense to increase the continuous ventilation rate for large unoccupied warehouse areas because this will increase operating costs and energy use without a significant benefit to the building’s occupants.
COMPUTER MODELING RESULTS
Combined Increased Ventilation & Stratification Comparison
- 4°F Stratification for Blow-Thru, Air Turnover*, Infrared 10°F Stratification for all other systems
- 30% higher than required A
- SHRAE 62.1 Ventilation (0.078 cfm/ft2)
Energy Consumption |
Gas (therms) |
Fan Electric (kWh) |
ASHRAE 90.1 Baseline |
35,608 |
78,483 |
Blow-Thru |
22,435 |
7,350 |
Draw-Thru |
29,214 |
8,950 |
Recirculation |
27,805 |
52,644 |
Unit Heater |
36,344 |
19,636 |
Air Turnover |
29,802 |
32,256 |
Infrared |
34,978 |
14,514 |
% Savings Vs. 90.1 Baseline
Blow-Thru |
37.0% |
90.6% |
Draw-Thru |
18.0% |
88.6% |
Recirculation |
21.9% |
32.9% |
Unit Heater |
-2.1% |
75.0% |
Air Turnover |
16.3% |
58.9% |
Infrared |
1.8% |
81.5% |
% Increase Vs. Blow-Thru
Draw-Thru |
30.2% |
21.8% |
Recirculation |
23.9% |
616.2% |
Unit Heater |
62.0% |
167.6% |
Air Turnover |
32.8% |
338.9% |
Infrared |
55.9% |
97.5% |
CONCLUSIONS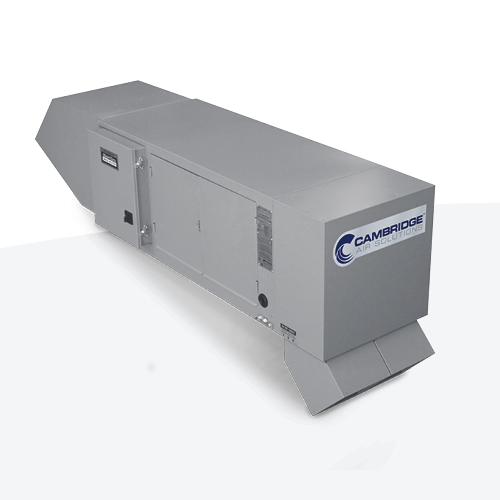
Figure 1
Computer Modeling
Predicted Energy Savings with Blow-Thru Space Heater
Other Industrial
Heating Systems. |
Energy Savings w/
Blow-Thru Space Heaters |
Indirect Gas-Fired Systems
Boilers |
53% |
Unit Heaters |
51% |
Air Turnover |
33% |
Infrared (Radiant) |
59% |
Direct Gas Fired Systems
Draw-Thru (Make Up Air) |
24% |
Recirculation |
28% |
1) Direct gas-fired, high temperature rise blow-thru space heaters used 35% to 38% less gas (therms) than the ASHRAE 90.1 baseline heating system for all cases included in this computer analysis. Using any other heater type increased the total therms required to heat the facility by at least 24% to 59% as shown in Figure 1. Blow-thru heaters use the least amount of energy to heat/ventilate large warehouses based on the following advantages of their design:
- Higher 92% efficiency vs. 80% rating for all indirect gas fired systems
- More efficient, variable capacity, modulating control burner
- Better performance from dual 160°F maximum temperature rise/ discharge temperature capability providing a high Btu/cfm ratio, which reduces the effective heating load relative to other direct fired heating systems.
- Electrical energy use is reduced by small blower motor, lower static pressure and ability to provide both space heat and temperedventilation using the least amount of outside air.
2) Air turnover, draw-thru make-up air and recirculation type heating systems outperformed the ASHRAE 90.1 baseline heating systems by only 13% to 22%.
3) Power vented unit heaters are a common way to heat warehouses and were found to virtually match the ASHRAE 90.1 baseline heating system for natural gas use.
4) Although infrared (radiant) heating is a good way to heat stationary objects and small facilities with open spaces, these computer simulation results indicate it to be a poor performer for large buildings that require both space heating and mechanical ventilation. Some manufacturers of infrared heaters recommend using their systems with a rated output 80% to 85% lower than the heat loss calculated by the ASHRAE Handbook or by turning down the room thermostat by an equivalent amount. This analysis did not incorporate either approach.
5) The ASHRAE 90.1 boiler baseline heating system had much higher fan (electrical) energy use due to the significant static pressure associated with using a ducted heating system for a large open area.
6) The combined effects of ceiling stratification and increased ventilation beyond ASHRAE 62.1 requirements can result in a significant 10% to 25% energy increase.
BEST PRACTICES GUIDELINES
The following guidelines are recommended for the selection of energy efficient space heating equipment used in warehouses and commercial/industrial buildings with large open spaces.
90+% EFFICIENT HEATERS
Select space heaters with energy efficiency ratings above 90% to get every possible Btu out of the fuel as usable heat.
Direct-Fired Blow-Thru Heaters
- 100% combustion efficiency (Ec)
- 92% thermal efficiency (Et)
CONSIDER VENTILATION AND IAQ
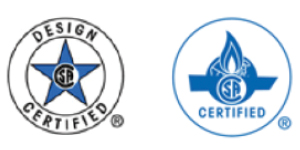
Be sure the heating system accounts for the facility’s ventilation and indoor air quality requirements. The use of direct gasfired, non- recirculating heating equipment certified to ANSI Standard Z83.4 is an energy efficient solution.
REDUCE STRATIFICATION
Reduce temperature stratification in buildings with high ceilings. Options include: small blow-thru space heaters with their high velocity vertical throw diffusers; large, low velocity constant air turnover heating units that provide two to three building air-volume turnovers per hour; infrared heating; or the use of ceiling fans.
Building Temperature Data Logging Graph
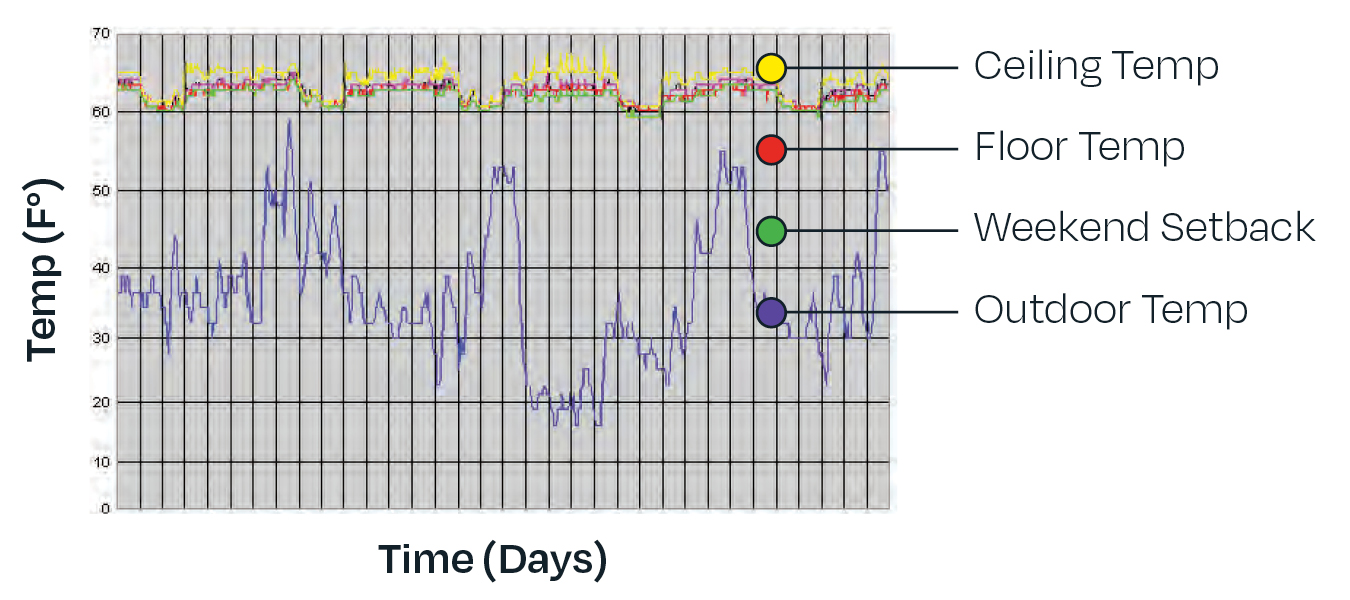
BE ASHRAE 90.1 COMPLIANT
Heating equipment should, at a minimum, be compliant with ASHRAE Energy Building Standard 90.1. As shown by this energy modeling report, this does not necessarily assure you are getting the most energy efficient heating equipment. But it is a requirement for many government tax incentives and utility rebate programs. It is also a prerequisite for LEED buildings. The heater manufacturer should have this stamped on their nameplate.
DOCUMENT ENERGY SAVINGS
Since actual energy savings are the real goal, use a proven technology from an experienced manufacturer that can document energy savings with studies of existing buildings and energy modeling.
If you’re interested in learning more about our technology, reach out to your local representative for further information!
DOWNLOAD WHITE PAPER PDF