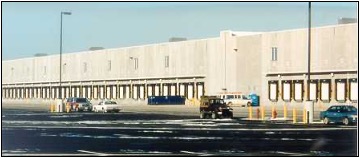
Target Albany Facility: 30 Years of Performance and a Data-Driven Approach to Decarbonization
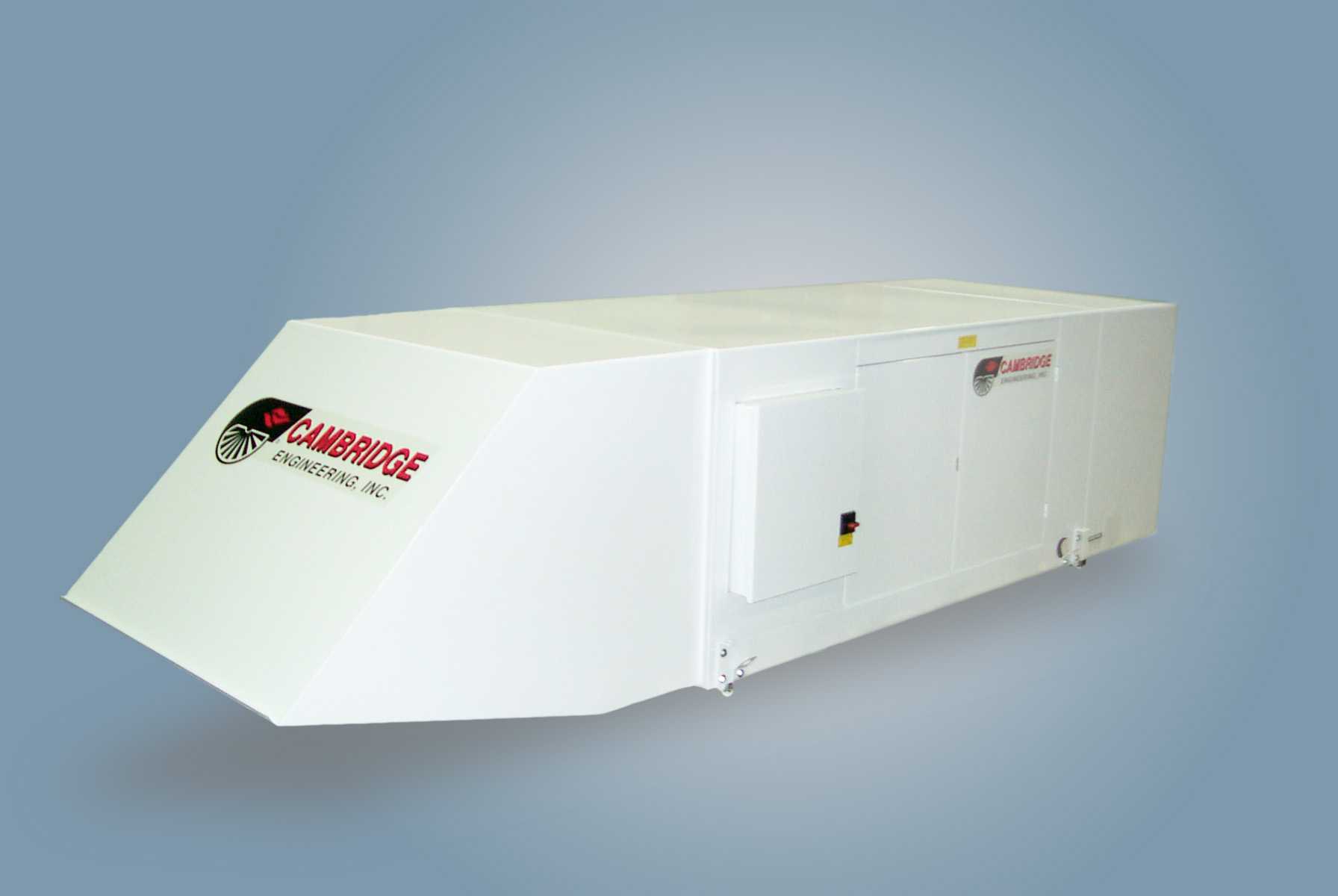
For nearly three decades, Target’s Albany distribution center has relied on Cambridge S-Series space heaters to maintain efficient and reliable heating. Originally installed in the mid-1990s, these custom painted white units have provided consistent performance with minimal maintenance. Now, after nearly 30 years of service, Target chose to replace the units with a direct, high-efficiency upgrade—a testament to the longevity and reliability of the original equipment.
Built to Last: Albany’s Direct Replacement
The decision to replace the aging S-Series units was based on their proven durability. Historical building studies from the 1990s highlighted the efficiency and effectiveness of these units when they were first installed, demonstrating a high-performance solution tailored for large distribution centers. Over the decades, these heaters have consistently delivered reliable heating with minimal maintenance, validating the original investment. Target opted for a direct replacement, ensuring continued reliability and efficiency without the need for a complete system overhaul.
Data from an old facility study provides additional insight into the performance of the heating system at Albany:
- Facility Size: 1.4 million square feet, with a ceiling height of 36 feet.
- Construction: R-14 Roof insulation and R-10 Walls, optimizing heat retention.
- Heating System Configuration:
- 14 units @ 2,200 MBH / 10 HP
- 3 units @ 2,200 MBH / 7.5 HP
- All units rooftop mounted.
- Operating Conditions:
- 21 hours/day, 7 days a week
- Design temperature: 55°F at an outdoor temperature of -6°F
- Thermostat setting: 59°F, with an average recorded temperature of 61°F
- Building Expansion: Added 240,000 square feet in 2002 to accommodate growing operational needs.
- Calculated Operating Costs:
- At an indoor temp of 55°F, estimated heating costs ranged from $0.10/ft² to $0.17/ft² depending on fuel prices.
Expanding The Story: Energy Efficiency Insights From Topeka and Ohio
Beyond Albany, Target is applying a data-driven approach to optimize energy use across its distribution network. An engineering analysis compared energy consumption at two nearly identical facilities—one in Topeka, Kansas, and another in Columbus, Ohio—to assess potential energy and cost savings.
Topeka, KS: This 1.2 million-square-foot facility was already equipped with Cambridge High Temperature Heating and Ventilation (HTHV) units. As the most energy-efficient heating system in the comparison, the Topeka site served as the benchmark for performance. Energy consumption data from this site was adjusted using heating degree days (HDD) to normalize for climate differences, ensuring an apples-to-apples comparison with the Columbus facility.
Columbus, OH: This matched facility used traditional draw-through units. By comparing its adjusted energy use against the Topeka benchmark, engineers estimated that converting the Columbus site to Cambridge HTHV units could reduce annual energy costs by approximately $177,000 and lower carbon emissions by more than 950 metric tons. Fan energy consumption would also be significantly reduced, aligning with Target’s broader carbon reduction goals.
This comparative analysis underscores the measurable benefits of Cambridge HTHV technology and provides a compelling case for future retrofits across Target's facility portfolio.
A Data-Driven Approach to Facility Optimization
Target is taking a strategic approach to optimizing its distribution centers, balancing reliability, energy efficiency, and sustainability. In Albany, longevity and minimal maintenance made direct replacement the right choice. In Topeka and Ohio, the focus shifts to carbon reduction and operational savings, leveraging energy analysis to guide future decisions.
Looking Ahead
By using data to inform facility upgrades, Target is identifying the most effective solutions for long-term operational efficiency and sustainability. Whether the goal is maximizing equipment lifespan or reducing energy use, Target has our lifetime support.
Want a carbon analysis done on your facility to see how much you could be saving on carbon and energy costs? Or want a Cambridge expert to walk a facility and provide personal insights and recommendations at no cost to you? We'd love to hear from you!
MECHANICAL CONTRACTORS: FIND YOUR REP
BUILDING OWNERS: SCHEDULE A COMPLIMENTARY WALKTHROUGH